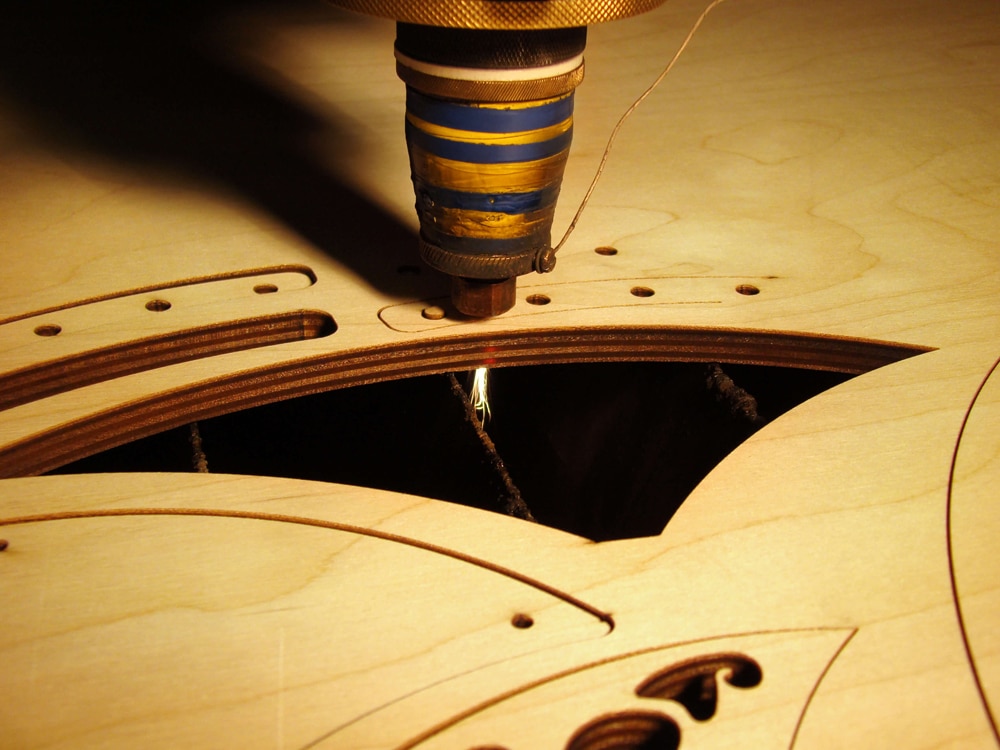
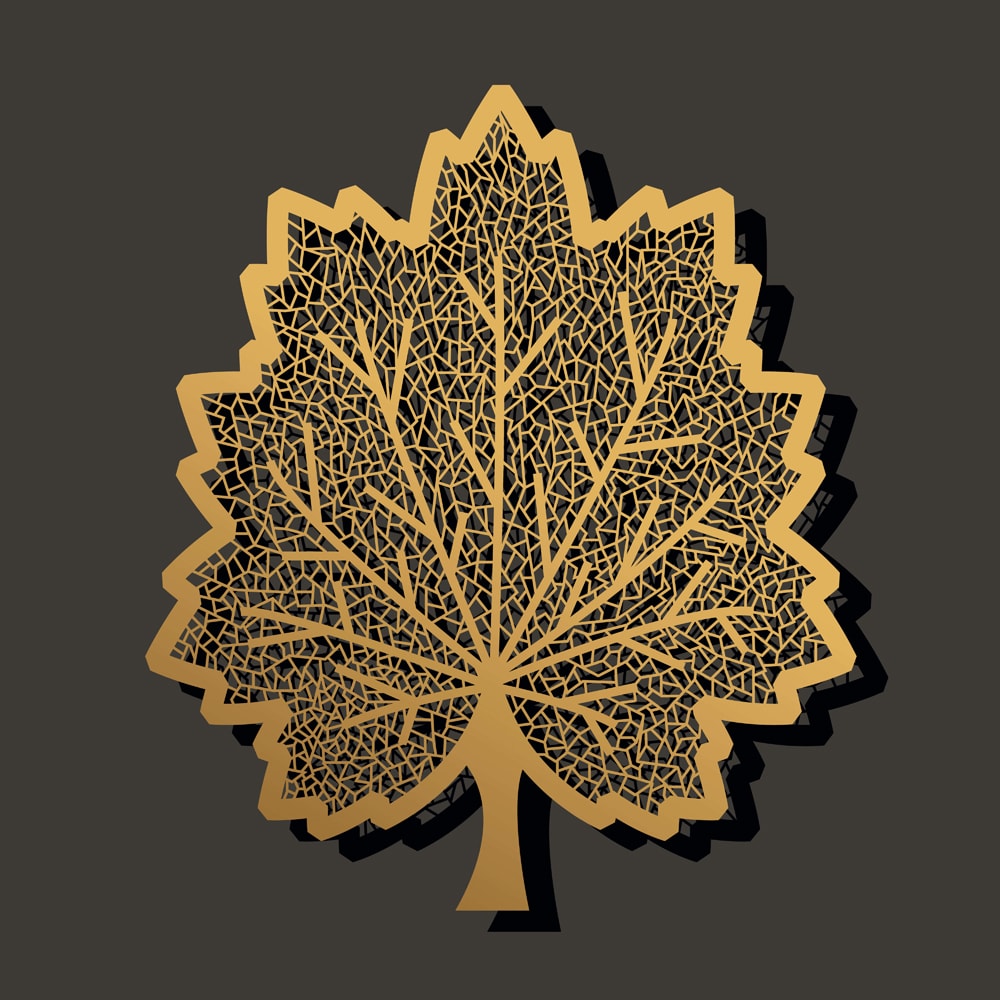
INDUSTRY USES
Laser & Waterjet Cutting Industry Clients & Customers
Waterjet & Laser Cutting Uses:
The following is information that we feel that you, our customer, will find helpful in understanding our Laser & Waterjet
cutting machining process and its capabilities. If you have any further questions, please contact our Sales
Department. We are happy to assist you in finding a service solution that fits your needs.
Machine Shops:
Allow us to pre cut your parts. We can hog out large or small parts with no heat affected zones. This will allow you to more tightly nest your waterjet parts in your mill, save milling time, save wear and tear on your machine, and save milling bits and other consumables.
Sign Companies:
We can cut you letters, marquees, banners or other artistic projects your customers want. We can waterjet or laser cut virtually any size and font you can imagine. Allowing us to cut out your letters and marquees can free up your valuable resources for assembly and installation. We can custom cut any font in acrylic, aluminum, stainless, wood or any other material your customer wants.
Artistic Designers:
If you can imagine it, we can cut it! We would love to help you create those artistic masterpieces. We can custom waterjet or laser cut virtually any material in any shape. Metal art is no problem for our machines. We can cut virtually any artistic design, from any material.
Metal Stamping and Tool Die Makers:
Eliminate tooling costs on short run parts by having cut with our precision waterjet cutting applications. Hard to stamp materials are no problem for our waterjet shop.
Angle and Channel Cutting:
Our angle and channel laser cutting capability enables us to offer massive cost and time savings to our customers on parts that would have normally required several complex operations. Our angle and channel laser cutting capability enables us to manufacture complete parts in one hit, which can be up to 90% faster than other conventional cutting processes such as sawing, milling, drilling and punching.
Tube Cutting:
Our tube laser cutting machine can cut tubes and profiles with large diameters and wall thicknesses without sacrificing productivity no matter how complex it might be and can laser cut tubes from 26 feet long with a diameter of up to 10 inches. A wall thickness of 1/2 inch can be easily achieved for mild steel. We also have the ability to tap or countersink tubes, angle and channel parts.
Metal Fabricators:
We can waterjet cut virtually any material up to 8 inches thick, and with tolerances of up to +/- .005”. Our waterjet machining can pre-cut your parts with minimum burr and no heat affected zones.
Manufacturing and Fabrication shops:
Allow us to pre-fabricate your parts, prior to your final process. Or, we can create your final product.
Torched or Burned parts:
Have a part that is too thick for plasma or laser cutting? We can waterjet cut that part and there will be no heat affected zones and no secondary clean up.
Reflective Materials / Fine Metals:
Reflective metals, as their name may suggest, are metals which can reflect back wavelengths that are directed at them. Examples of these metals are copper, brass, and bronze. Some of the most reflective metals are aluminium, gold and silver, the latter of which can reflect around 95% of visible light.
This poses an obvious problem for the laser cutting process, which involves a laser beam of heat and light. We can solve this problem by cutting your reflective metal project on our state of the art Fiber Lasers.
Aerospace Industry:
The aerospace industry is another industry in which the laser cutting process is extensively used. It’s extremely similar to the automotive industry in that in contains the design, development, production, manufacture, marketing and selling of thousands of different parts, processes and people involved.
The difference with the aerospace industry is that this is all done on a much larger scale and the resulting products need to withstand a great deal more pressure. With this in mind, the processes involved need to be even more precise and reliable, which is why laser cutting finds such widespread use.
Auto, Motorcycle, ATV Enthusiasts, and
other Hobbyists:
We are right there with you!! Sometimes you just need that one special thing made. E-mail, call, use our instant quote software or stop by. Well help you out! If we can’t do it, we’ll help you find someone that can!
What is a Waterjet Cutting Service?
Abrasive jet and Waterjet technologies have been around for years. Waterjet cutting has been a specialty technology used in a wide variety of industries since about 1970. Around 1993, big advances in the technology were introduced that have caused this technology to become very popular for machine shops. A waterjet is a tool used in machine shops to cut virtually any material with a (very) high-pressure stream of water and abrasive.
This odorless, dust-free and relatively heat-free process can also cut something as thin as five thousandths of an inch. The tiny jet stream permits the first cut to also be the final finished surface. This single cutting process saves material costs and machining costs. For example, the engineer merely gives a gear drawing to the cutting shop via usb or e-mail and gets the finished gear back.
Waterjets cut softer materials, while abrasive jets are used for harder materials. The actual cutting is often done under water to reduce splash and noise. Faster feed rates are used to prevent the jet from cutting all the way through.

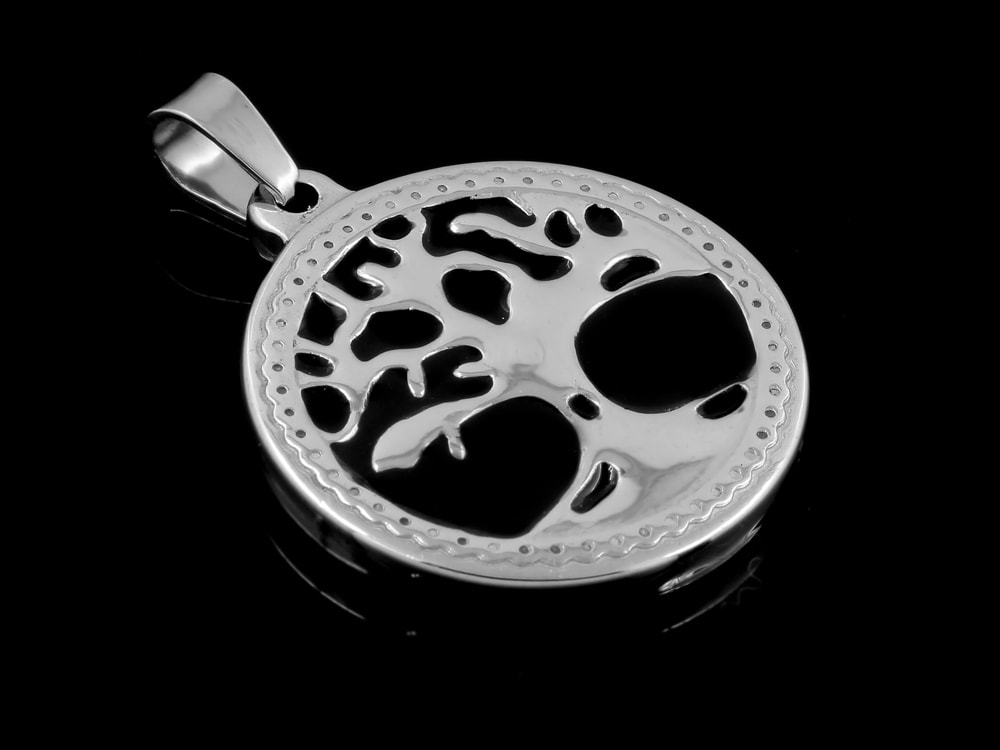
Application Advantages of Laser Cutting
Laser cutting is a manufacturing process which can eliminate the need for machining on many engineering jobs, enabling you to save money on manufacturing costs.
Laser cutting presents certain advantages over plasma cutting as this process is more precise and uses less energy when cutting steel and aluminum sheets. In addition, our latest Fiber laser machines, such as our 8Kw machine, are now approaching plasma machines in their ability to cut through thick materials.
The precision levels and edge quality achieved with laser cutting machines are better than traditional cutting methods, as the laser beam will not wear during the laser cutting process. Laser cutting technology also enables us to cut complex shapes without the need for tooling and at a similar or faster speed than other cutting methods.
The fact that laser cutting technology offers reduced contamination of the workpiece presents certain advantages over traditional mechanical cutting techniques.
Laser cutting also allows us to cut small diameter holes with complex detail and good edge quality in either sheet, plate, tube or box section.